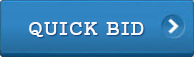
What is Injection Molding?
Injection molding is a commonly used and highly versatile method for manufacturing various products using an injection system and an injection mold. Injection molding is capable of producing products of varying complexity, size, and function from many materials. The materials most often used are metal, glass, and plastic polymers, though plastic is used significantly more often than any other material. For example, injection molding is used to create Legos, Frisbees, blender bases, car door panels, keyboards, and thousands of other plastic parts.
Injection molding is, perhaps, the most cost-effective method for fabricating products and plastic parts because it uses injection molding machines that are efficient with both time and materials.
Who Uses Injection Molding?
Injection molding can be used by anyone who would like to create a unique part. Typically, an injection molding company performs plastic injection molding for manufacturers who may need one or more pieces of a larger product molded and then assembled. Some injection molding companies offer assembly services before shipping a product back to a manufacturer, though many manufacturers gather injection molded parts and other materials at their base locations for assembly.
What are the Steps to the Plastic Injection Molding Process?
The plastic injection molding process is similar for every injected part made in the injection molding industry. Because injection molding is dependent on the shape of the part, most often custom injection molding is required. The following are the steps performed by injection molding companies.
- 1. Design
Designing a plastic part correctly is essential to its success. A designer creating parts must take into account the type of injection molding plastic that will be used, wall width and stability, as well as overall performance of the part or larger product. Today, injection mold design is primarily completed using 3-D modeling software that can perform virtual tests on the finished part. Once the design is considered sufficient for the part, the dimensions are used to create a custom injection mold.
- 2. Mold Making
Custom injection molds are made from different metals, depending on the type of part being injected. Some people claim that one kind of metal mold is better than another for molding; however, it’s most important that the mold will stand up to the number of parts that will be in the run and that the metal used can be formed to the exact specifications of a part’s design. If plastic injection molds are off by even a fraction of an inch, the parts could be entirely useless. Injection mold making has to be very precise. In some cases, injection molding inserts can be used as interchangeable parts to make variations of the same parts.
- 3. Clamping
Before parts can be injected with plastic, molds have to be fitted into the injection molding machine. When molds are put into molding machines they must be tested to make sure they shut correctly during injection. This prevents plastic from leaking out the sides of the mold and ruining the part. Different machines are required, depending on the part because they have different clamping pressures; larger parts require higher pressures.
- 4. Injection
Injection is the key step in the process. During injection, molten plastic is pushed into the mold using a barrel heater and a screw. The screw is forced forward using hydraulic pressure, and the tip is programmed to only insert the correct amount of plastic to fill the mold, closing off between parts.
- 5. Cooling
Cooling the part at the right temperature for the correct amount of time will make a perfect part. If performed incorrectly, sections of a part may shrink or warp, destroying the part. Cooling is also accompanied by pressure to keep the plastic from shifting in the mold. Most molds only need to be cooled for a short amount of time (only a few seconds) before parts are ready, but others can take up to a few minutes.
- 6. Ejection
When plastic injected parts have cooled sufficiently, they are ejected from their molds. Some are ejected carefully to allow further cooling, and others are ejected nonchalantly into crates of hundreds of parts. Quality injection molding companies will check parts for damage or incorrect molding immediately to ensure that their equipment is performing properly.
Injection Molding vs. Blow Molding
Injection molding and blow molding have different strengths. For example, injection molding products are usually not made as hollow parts with uniform interiors the way blow molding products are. Injection molding is capable of creating solid products in a very precise mold. Blow molding creates hollow products in molds that only detail the outside of the product.
Neither method of molding is acknowledged as generally better than the other because they are specialized for various parts.
Streamline Plastics Delivers High-Quality Custom Injection Molding
Streamline Plastics, a Streamline company in Utah that focuses solely on injection molding services, offers customized help on every step of the injection molding process. The staff is highly trained and certified in molding techniques, and every product is checked for quality at the time of ejection. Streamline Blow Molding is another Streamline company that focuses more on blow molding, creating quality bottle products at an affordable price.
If you are looking for a place to complete your injection molding, Utah is just a click away. For more injection molding information or for a free quote on your next injection molding project, contact Streamline Plastics at (801)782-3660.