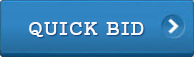
What is Blow Molding?
Blow molding is a manufacturing process by which hollow plastic parts, such as bottles, are formed in a blow molding machine. In general, there are three main types of blow molding: extrusion blow molding, injection blow molding, and injection stretch blow molding.
All types of plastic blow molding are essentially the same; however, some methods are more effective for certain parts, whether due to the shape or number of parts in the run. Some blow molding companies may offer different types of blow molding based on their available equipment.
Blow Molding: How It Works
Blow molding is an important industrial process for making hollow plastic parts in custom blow molds, such as blow molded bottles. Blow molding technology is borrowed from the glass industry, with which plastics compete in the recyclable or disposable bottle market.
The blow molding process involves a number of steps, simplified in this list.
- Storage. Plastic in granular, pellet form is stored in a hopper for future use.
- Heating. The plastic granules are fed through a heated section of a blow molding machine.
- Forming. The plastic granules melt into liquid which is formed into parisons.
- Blowing. Pressurized air is forced into parisons which forces the plastic to the sides of the blow molds, making the shape of the bottle or plastic part.
- Cooling. The bottle is cooled and released from the mold.
The distinctive part of the blow molding process is the plastic parison. The parison is a tube-like piece of plastic with a hole at one end, shaped much like a test tube. Through the hole, compressed air can pass into the plastic parison. The parisons are clamped into blow molds and air is forced into them, which pushes the plastic out to match the molds. This is why the process is called blow molding.
Blow molded parts are only manufactured from thermoplastics, most often from Polyethylene; it has a high density and molecular weight ideal for blow molding.
Extrusion blow molding is organized as a high-production bottle blow-molding operation. It is automated and often combined with further processes such as labeling or bottle filling.
Injection blow molding is slightly different because, in this process, the starting parison is injection molded rather than extruded. The steps are as follows:
- Parison is created around a blowing rod using injection molding.
- Parison mold is opened and parison is transferred to a blow mold for the main objective.
- Parison is inflated with pressurized air to fit into the shape of the blow mold.
- The finished product is removed from the blow mold.
Using the different blow molding processes for blow molding plastic bottles all essentially create plastic bottles, but each method may take different equipment. Some blow molding companies may also be able to perform custom blow molding. Custom blow molding products may consist of special bottle styles, added logos, colored bottles and various plastic choices.
Blow Molding vs. Injection Molding
Blow molding and injection molding are very different procedures that are capable of producing significantly different products. Blow molding products usually consist of hollow bottles, whereas injection molding products can be any type of plastic product from a plastic bead to a car door panel.
Blow molding products rely on pressurized air for creation; this creates uniform parts that may or may not have seams. Injection molding only uses poured molten plastic to create its products. Blow molding also relies less on mold making to determine the strength of the part than injection molding does.
Blow molds usually only determine the exterior form of the product. Injection molds have to include every facet of the product, such as wall thicknesses, center shapes, and any other important attributes, making the mold more than 90% of a part’s success.
Blow Molding Advantages
Depending on the part that needs to be created, one type of molding may be preferable over another. Advantages of blow molding include less time spent on the mold-creation process and faster turn-around times by a custom blow molding company. Blow molding is well suited for high production rates using a variety of materials. Blow molding tools are also fairly inexpensive compared to other molding equipment, so more companies are able to perform custom plastic blow molding with custom blow molds.
Streamline Blow Molding Offers Custom Plastic Blow Molding
Streamline Blow Molding, a Streamline company, has all the equipment and manpower to create exceptional blow molded products. They offer customized options for blown products such as logo inclusion and color changes. Streamline Blow Molding is proud of their clean processes, recyclable materials, and fast production.
Streamline Plastics, another Streamline company, provides injection molding services for other turn-key plastic products. To learn more about their blow molding services, or for a quote on your next blow molded product, contact Streamline Blow Molding today at (801)782-3660.